How to secure FMCG supply chains with traceability?
Publié le 2 octobre 2019 dans Brand Protection
The need for precise traceability
In Russia, vodka producers have to comply with a recent government directive on serialization (no. 2592). This mandates that manufacturers of alcoholic drinks must label each unit produced with a serialized tracking label. During production, the data must be registered at different packaging stages. The registered data is then fed into a government database.Our solution with direct database connectivity
Together with our integrator, we have designed a system to ensure traceability in a fast-moving bottling line. This includes multiple MicroHAWK ID-40 readers. The ID-40 is the smallest IP65/67 rated true industrial Ethernet barcode reader. It provides best-in-class decoding for 1D/2D or DPM codes and has a rugged, ultra-compact case. It’s very easy to install and to use. Our FH camera system is ideal if there is a need to read additional the labels for example on the bottle caps.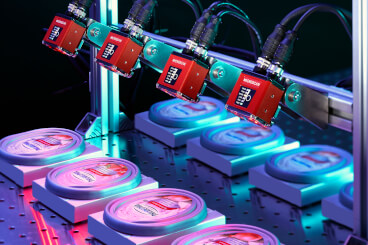